What are high performance pigments?
- By Centre Colours
- •
- 22 Oct, 2018
- •
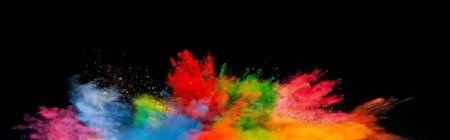
High performance pigments do more than their name suggests. While they are quality pigments, their purpose is more to do with the high performance properties within them than the finish itself.
That being said, of course, a key consideration is how the pigment appears. This means the basic properties of the pigment itself need to be of a high quality - which is where our pigment dispersion process shines. The result is a stable pigment capable of being manufactured with high performance pigment elements.
The characteristics of a high performance pigment usually depend on the application - and the person you ask! To quote Ink World magazine :
“The three essential elements of a HPP are excellence in performance, persistence in application and high value-added economics for all parties in the supply chain. HPPs are those pigments that exhibit very good to excellent properties of persistence. That is, they have resistance to light, heat, humidity, organic solvents, water and detergents.”
High performance pigments are also summarised using the “three E’s”, as defined by Gunter Buxbaum:
● effectiveness (technical performance)
● economy (benefits to the customer)
● ecology (environmental and toxicological safety)
The most prevalent of the E’s mentioned above is effectiveness. Depending on the industry you’re in, an effective high performance pigment could be many different things.
For example, in the automotive industry, a high performance pigment is needed to withstand extreme weather conditions - just think of the extremes we’ve had in the UK over the last 6 months, where pigments have to cope with high UV levels and being covered in snow - whilst delivering the excellent finish you’d expect on a vehicle.
The same is also true for the plastics industry. High performance pigments are a necessity when producing plastics that will be exposed to the elements, such as PVC pipes, window profiles, vinyl siding, and gutters. HPPs ensure that not only the colour of these is consistent across large quantities, but also stand up to the test of high levels of heat (and therefore flexibility in plastics).
However, we think there’s more to a high performance pigment than this. In recent years we have worked with clients to integrate innovative elements into pigments, such as graphene.
Graphene is known for its highly conductive properties, but it’s only when you see these applied that you recognise the effect they can have. For example - used in a commercial setting, the use of graphene pigments in paint can result in less heating and air conditioning being required in office environments, as graphene absorbs heat before radiating across its entire surface.
Another example of graphene being used within a high performance pigment is its application in the maritime sectors. As graphene is resistant to corrosion, this can result in ships with corrosion-resistant hulls, and off-shore wind towers that also withstand the elements.
This goes to show that a high performance pigment truly is dependent on the outcome you’re looking to achieve. With so many possibilities, often the most essential element of developing a high performance pigment is finding a partner with the capability to match your vision.
We work with our clients to develop truly innovative coatings, direct from our Leeds-based HQ. For more information, please don’t hesitate to get in touch with the team at Centre Colours.